Getting ISO 13485 Certified in Nogales, Arizona (AZ)
Contact Us
Working as a manufacturer or a company involved in the supply chain won’t be a ‘piece of cake’. After all, there are many regulations to meet if your company is in Nogales, Arizona, starting with standards like ISO 9001, ISO 13485, and many others. If you have ever wondered how companies are able to offer high-quality products or top services, you must know the main reason is that they have done their homework properly.
But for those that do not deliver customer satisfaction and only offer poor items and results, it is very clear what went wrong: they didn’t follow legal regulations nor invested in improving their processes. At IQC The ISO Pros, we understand it isn’t simple to invest in several regulations or norms, but it is necessary and you cannot avoid doing it.
This is why we encourage you to focus on the ones you need and start working on them as soon as possible. Now, where can you start with them? That depends on the company you own, its size, type, and activities or processes. Although many generic standards and norms are implemented in any company regardless of the previous aspects, many others are only for a group of them.
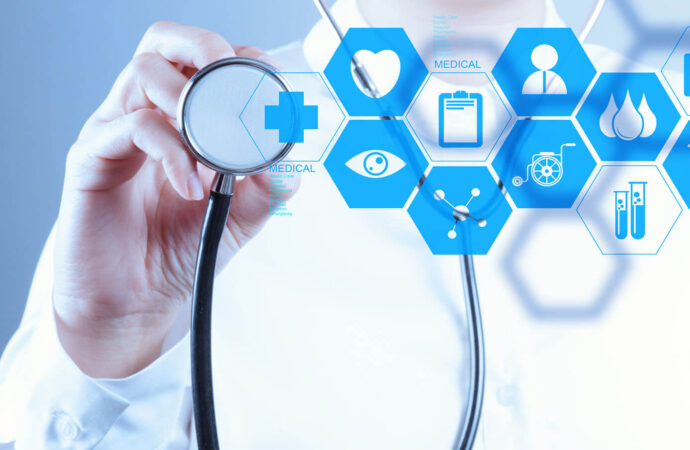
In the beginning, we mentioned ISO 9001, which is the main and general quality management system standard. For manufacturers or companies in the supply chain, ISO 9001 is a mandatory standard that provides all the guidelines to design, establish, maintain, and improve their quality management systems. With what purpose? To meet customer satisfaction, improve processes, and obtain high-quality products for the public.
With that said, you can include this standard in particular to your ‘must-have’ list in order to start with it. Now, what’s next after you implement and get certified in it? Start looking for those that are more specialized for your company. For medical device companies and manufacturers, there’s a similar ISO that needs their attention since it provides more requirements for the products manufactured and offered in the supply chain of this industry.
ISO 13485 is a quality management system standard for medical device companies only, and it establishes specialized guidelines and requirements to ensure they meet customer satisfaction, can provide high-quality devices, and ensure those won’t disappoint in their performance. Unlike generic standards, you need to be very careful in harmonizing your company’s needs with the guidelines in the ISO.
Why? Because if it isn’t done properly, the outcomes won’t be the expected ones since ISO 13485 goes for the QMS, but instead of focusing on customer satisfaction alone, it is more about the documentation and safety requirements. We at IQC The ISO Pros, can provide you all the assistance and help required to start implementing it and obtain your certification in Nogales, Arizona, or any other city in the state.
What you must know about ISO 13485?
Before you start implementing a standard, you definitely need to know everything about it but also, about your company. However, we want to focus on the ISO itself and what you should expect from its implementation. Since ISO 13485 is the main quality management system standard for medical devices, you will have to implement it from the very beginning. Something most companies don’t know about ISOs is that they can be mandatory or voluntary. In the case of this one, it is completely mandatory for any medical device organization.
But what we want to highlight the most is the fact that you won’t only meet its requirements to obtain the certification but also fulfill other legal regulations. ISO 13485 addresses many regulations and norms from other documents and law restrictions. As a result, you are able to have control over every legal aspect and finally operate freely and without worries. If you are a medical device company that has been operating for months or even years but haven’t met the requirements in this ISO, we find it hard to believe you’re still in business. However, if you are and haven’t put too much attention to it, we encourage you to do it right now.
Since the standard can be implemented no matter the size of your organization, you can start whenever you want and feel prepared for it. With that clear, here are two aspects you need to know about ISO 13485:
- Although it is a quality management system standard, it isn’t focused on the product itself but rather on the processes to obtain the devices so you can control and improve them to obtain the desired results when manufacturing the products.
- Unlike other standards, an individual can’t get ISO 13485 certified but only be a person who helps to obtain the certification. The ISO was created only for organizations that are established in the medical industry.
What are the differences between ISO 9001 and ISO 13485?
The main difference is the fact that ISO 9001 can and must be implemented for any organization regardless of its size, product, service, or industry. There’s no requirement to implement it. Since it is a general standard, it offers guidelines with different approaches to achieve the desired results. Meanwhile, ISO 13485 is entirely focused on the manufacture of medical devices, which is why we consider it to be a specialized standard for the companies in this industry.
The difference in the approach, guidelines, and significant focus on the quality management system to obtain high-quality devices is quite a lot when compared to the previous ISO. First, we have to point out how ‘inflexible’ it is since the focus on regulatory compliance is quite fixed in only a few options. What are we trying to say with this? That the organizational process is less flexible and needs to be met with very specific methods and requirements. You can’t expect a generic standard to be just the same as a specialized one since there wouldn’t be a good reason to get certified in both of them.
But what happens with the goal of establishing, maintaining, and improving the quality management system of the company? Isn’t it the same? Don’t get us wrong, both standards have significant similarities that will make you feel—at times—that you are implementing the same standard. But when you focus on your medical device company’s needs and harmonize them with ISO 13485, you will notice it addresses them much more and focus on finding solutions but also preventing any incidents that could take place.
Going back to the last question, the system may be the same, but the way to guarantee customer satisfaction and achieve the outcomes is different depending on the company. While ISO 9001 is perfect to have a good concept of how the QMS should be, ISO 13485 specifically addresses the need of the device manufacturer for maintaining the effectiveness in the system and guaranteeing that all the devices or products will meet every requirement and cover everyone’s needs. Instead of looking at this medical device standard as something similar or completely different, we suggest you keep in mind the fact ISO 13485 was build based on the requirements of ISO 9001. Therefore, we assure you will go in the right direction, but to deliver the best and work on the processes of your medical device company you need to focus on its needs and activities in specific, not like you were any other company in any other industry.
What are the benefits of implementing ISO 13485?
It is hard to see the benefits when you are focused on implementing it as a mandatory requirement for you, a manufacturer, to continue in businesses. However, you must know that every standard comes with benefits for the company outside of the clear requirements that need to be fulfilled. At IQC The ISO Pros, we highly recommend you pay attention to what you will gain from it instead of investing all your energy in the “I need to implement it no matter what”.
A very common mistake is to consider ISOs something you cannot avoid and need to “waste” time and resources in when all of them are actually part of the best additions you can have for your organization. With that said, what benefits should you expect from this one in particular? Well, since ISO 13485 goes for the quality management system, you will notice a great improvement in all the processes. Keep in mind it isn’t a standard that aims for the product but rather all the policies, processes, and activities involved in manufacturing the device, which leads to having a more efficient and effective production.
As a manufacturer, you always want to improve your processes to spend less money, time, and resources in acquiring the same product or even a better one. Therefore, it is safe to say that the main benefit is to achieve a quality management system that allows your company to achieve efficiency, effectiveness, and reduce the resources used for the devices. With this alone, we are sure you will be able to earn more than you have been able to do so far, and your workers will also be happy that you made their job easier and less exhausting.
On the other hand, extra benefits aim for other aspects, such as:
- Reduce safety and legal risks while creating the device.
- Economical work processes.
- Safer and economical work environments.
- Get recognized in the industry.
- Be more competitive among other companies in the state and internationally.
- Guarantee continual improvement, which leads to the growth of your organization.
Where to start with ISO 13485?
The process of implementing a standard takes time and resources. However, we don’t want you to feel overwhelmed with all the things you need to do to finally fulfill every requirement and obtain your certification. ISO 13485, unlike others for the same management system, is easier to implement thanks to the straightforward guidelines it establishes. The ‘issue’ with it is the fact that medical device organizations need to be completely aware of their needs and goals to harmonize them with the standard. And let’s not forget to harmonize the ISO with ISO 9001 as well since, by the time you go for ISO 13485, you should be certified in the first one.
With that clear, the standard and its guidelines start with management support and identify your customers' requirements for the quality management system. In this way, you will aim for the right objectives while implementing the standard and ensure you definitely meet customer satisfaction with the final result of your devices. Next, here’s something that you might not know: ISO 13485 is also about documentation. Unlike what it seems, many standards aren’t about taking action and dealing with processes alone. Instead, they also set requirements and guidelines for the documentation in certain aspects.
In this case, your medical device company needs to develop documentation that includes a Quality Policy, Quality Objectives, and Quality Manual. With these documents, you will have pretty much a way of implementing the quality management system of the company focused on the medical device industry. There’s a lot of paperwork involved in its implementation, but as tough as it seems, they are required to achieve the desired outcome. A long list of mandatory documents is established by the ISO and with our help, IQC The ISO Pros, you can start creating them in order to have everything in order.
We highly suggest you start with the documentation since it isn’t only what the guideline establishes but also the best way to approach the rest of the implementation. After all, from here on, it is necessary to take action, change processes based on the new documentation, and meet requirements.
What requirements does ISO 13485 establish?
It is hard to go over all the standards here and now, but it is possible to have a clear overview of what to expect when trying to get certified. The structure of the document is split into 8 sections, where sections 1, 2, and 3 are completely introductory for you to understand the purpose and goal of the standard.
From section 4 to 8, you will start working on the mandatory requirements for the quality management system of your medical device company:
- Section 4 – Quality Management System: this section goes for the documentation and general requirements for the QMS, which just confirms what we said before about where to start with the ISO. Since
- Section 5 – Management Responsibility: addresses the need for top management that helps to guarantee customer satisfaction and the improvement in the quality management system and ensure its implementation but also, maintenance.
- Section 6 – Resource Management: focuses on the need of having control over all the resources in the company, including human ones, infrastructure, and others that can be considered part of them.
- Section 7 – Product Realization: focuses on the steps during the planning and creation of the products, in this case, medical devices to ensure they meet the quality expectations and requirements and, of course, meet customer satisfaction.
- Section 8 – Measurement, Analysis, and Improvement: can you maintain and guarantee that your QMS continues working properly and proves to constantly improve? The requirements to make this possible are established in this section of the standard.
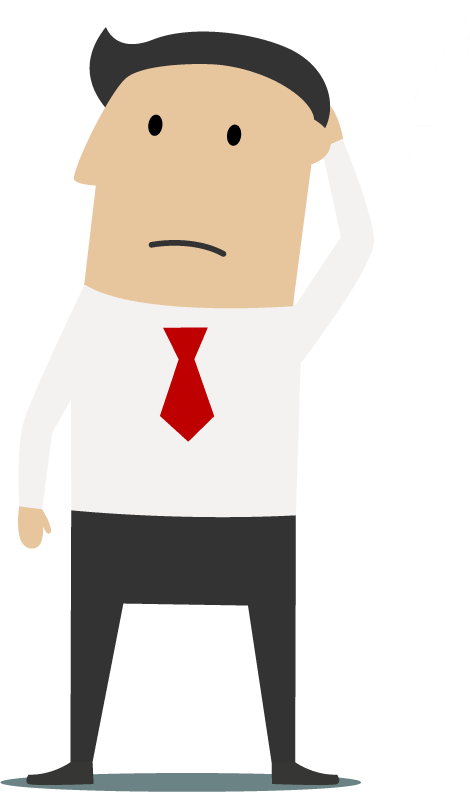
How to start implementing it and get certified
Our company, IQC The ISO Pros, is ready to help you with all the processes of understanding, implementing, and getting certified in ISO 13485. We have been in the ISO industry for over a decade. During all these years, we have helped over 100 different medical device organizations to implement the standard and be updated after every revision.
How is this possible? Because we don’t offer implementation services only, instead, we aim for training and consulting services as well. We want you to be prepared for everything that is to come and since it is impossible to maintain your processes and products without understanding the ISO and regulations you’re implementing, training you sounds like the best option. Of course, you can access any of the services individually or at once depending on your needs.
We understand some companies aren’t looking for a company that trains them but rather just takes care of the entire process. While others want to know it all in order to understand what they are signing for. Whatever it is or the service you are aiming for, we will be there for you.
Our services are available in Nogales and all over the state of Nogales, which means you don’t have to worry about us not being available or near to your company. We understand many medical device manufacturers are struggling, which is why we wanted to be there no matter the place and circumstances. This means you can start implementing ISO 13485 with us, get trained by our professionals, and obtain your certification after the audit without thinking you might not have fulfilled every requirement established.
Just contact us and we are sure you will find what you need with us for this ISO, be its implementation, training, or just simple but very crucial advice.